Die bond soldering
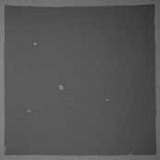
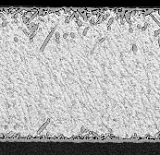
In power electronics the solder joints between the power dice and the substrate (e.g. DCB) have to be totally voidless in order to achieve a good thermal path. One possibility to solder the power dice is to print solder paste on the substrate and place the dice into the paste before soldering is performed in an oven. The advantage of this technology is that the dice adhere very well to the substrate. Thus the application of condensation soldering where vibrations are heavy is possible. However, the application of solder paste implicates that voids are formed in the solder joint which have to be removed using a vacuum process step. The flux residues have to be cleaned after soldering, too.
Other soldering technologies are based on the usage of solder preforms. At IZM a die bond soldering technology has been deveoloped in which neither is flux applied nor is vacuum necessary to achieve voidless solder joints. Using SnAg3.5 preforms power dice of an area of (12,5 × 12,5) mm2 were soldered to BCB substrates. Voidless solder joints were achieved without applying flux and without applying a vacuum step. The most important point is that there are no voids produced during the soldering process. Void formation is due to gases entrapped in the solder joint, due to a substrate metallization which shows poor wetting or due to the presence of oxides on the solder.
Although voids can be removed by applying vacuum, poor wetting cannot be overcome and oxides are not removed in vacuum. Thus it often happens that after applying vacuum areas are found in which there is no real connection between the solder and the metallization even though the joints appear voidless using x-ray analysis. Such imperfect areas in solder joints are not detectable by using x-ray analysis but with ultrasonic microscopes only and are detrimental in terms of thermal performance and reliability.
It could be shown that this die soldering technology can also be applied to very large areas. Voidless solder joints between DCB substrates and Cu coolers were achieved. For very large solder joints vacuum is applied to remove voids caused by entrapped gases only. Also, this technology has been proved compatible to production equipment.
Another approach towards voidless solder joints is the so called die bonding using capillary force. The solder is placed beside the die on the substrate. As soon as the solder is melted it wets the substrate and due to the capillary forces flows beneath the chip. Almost voidless solder joints could be realized using this technology using neither flux nor vacuum [Patent DE 102 52 577].