Thermoforming under high pressure instead of vacuums
From films to interactive touchpads in seconds
Fraunhofer IZM has more than 25 years of experience with integrating the tini-est of electronics reliably into many types of materials, including thermoplastic films. The Institute’s researchers now have access to a machine that can create highly customized shapes in record time for use in advanced display or control devices.
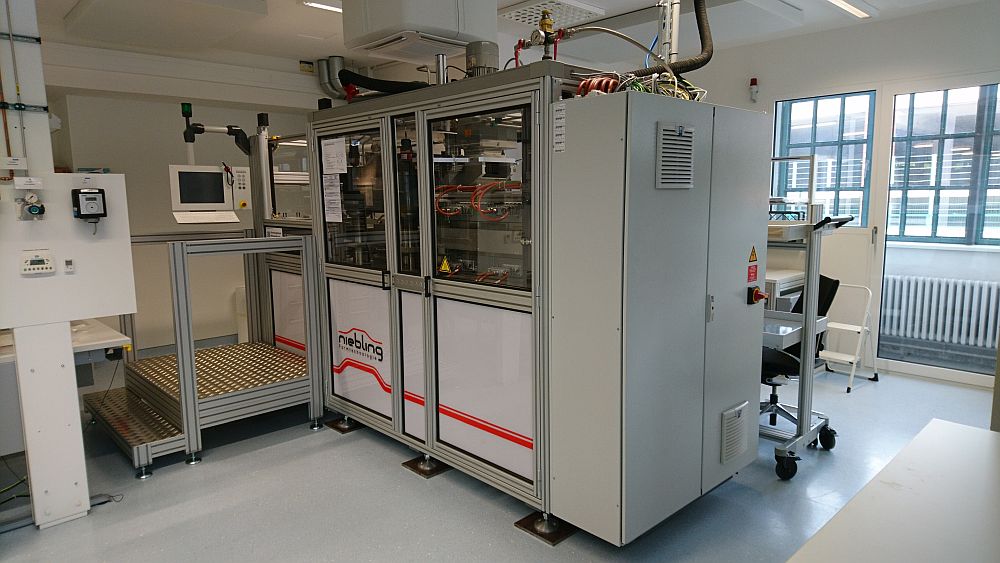
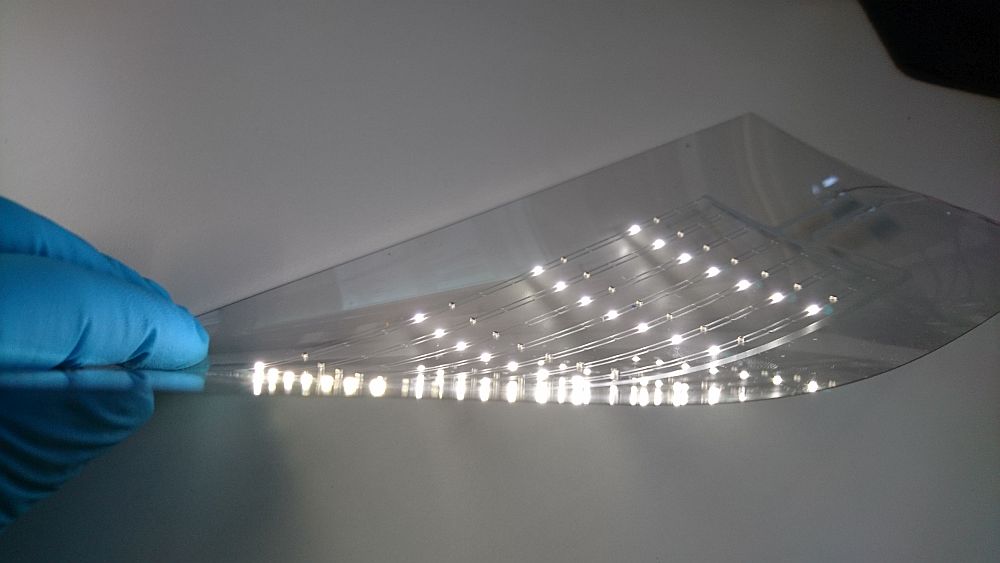
Capabilities and Technology of the Niebling SAMK 650:
It takes mere seconds and just three process steps for the Niebling SAMK 650 to give thermoplastic films a new shape. The original films are fed into the machine’s insertion station; a carriage moves the film into the heating chamber, where it is heated in a contactless and fully configurable process. The secret: The output of the ceramic heating units can be adjusted specifically for each substrate to match each customer’s needs. By contrast to conventional vacuum forming processes, the Niebling SAMK 650 works by high-pressure thermoforming, using air that is heated and brought to up to 80 bar of pressure. This guarantees exceptional repeatability for the process, as the material to be formed only has to be heated up to the softening point and no higher. The softened thermoplastic film is moved into the heart of the machine, where it is formed with a tool designed to the customer’s specifications. A toggle lever presses the film onto the form, where the hot and pressurized air gives it the desired contours. The finished piece then returns, cooled and in its new form, to the insertion station.
Applications and Active Projects:
Compared to vacuum forming, the Niebling SAMK 650 can shape and form smooth films that are equipped with conductors or other electronic components into extreme geometries. The resulting smart units can be used e.g. in household goods like washing machines, stoves, or ovens to enable cutting-edge applications. The machine is already being used in the current CoMoDo project at Fraunhofer IZM to produce prototype controls for washing machines with integrated touch functions. The researchers at the Institute will continue to pursue the project’s goals with their partner PAS Deutschland GmbH until the end of 2020. Other possible applications can be imagined in the automotive industry, e.g. adding exclusive touch controls to centre consoles, or in medical technology, where e.g. smart implants need to be fitting with sensors.
Limitations:
Any machine has its limitations: The forming tools used in the Niebling SAMK 650 must not create a constricting shape, as the finished piece could not be removed from the tool. Any complicated shapes or shapes that require the film to be extended for more than six centimetres also require manual adjustments at the machine.
Fraunhofer IZM is always available for queries about possible cooperation, more information about current projects, or the Niebling SAMK 650 itself:
Contact for the Niebling SAMK 650:
Manuel Seckel l phone +49 30 46403-740 l manuel.seckel@izm.fraunhofer.de
Contact for processes and lamination:
Joao Alves Marques l phone +49 30 46403-651 l joao.alves.marques@izm.fraunhofer.de
Last modified: