Currently, interconnection processes in e-textile production, especially in industrial manufacturing at SMEs, still pose a major challenge, as such electrical contacts are usually made by hand soldering, rigid connector assembly and other manual techniques. The result is an enormous amount of manual labour, which massively increases production costs in high-wage countries and slows down economic growth in the market segment dominated by SMEs.
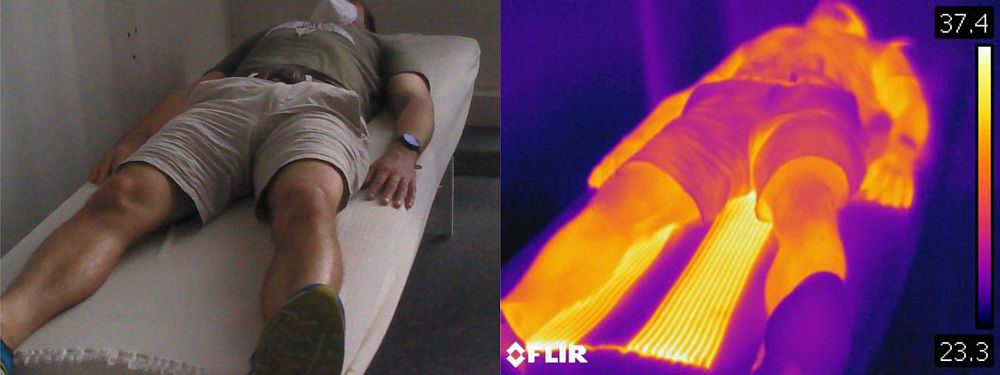
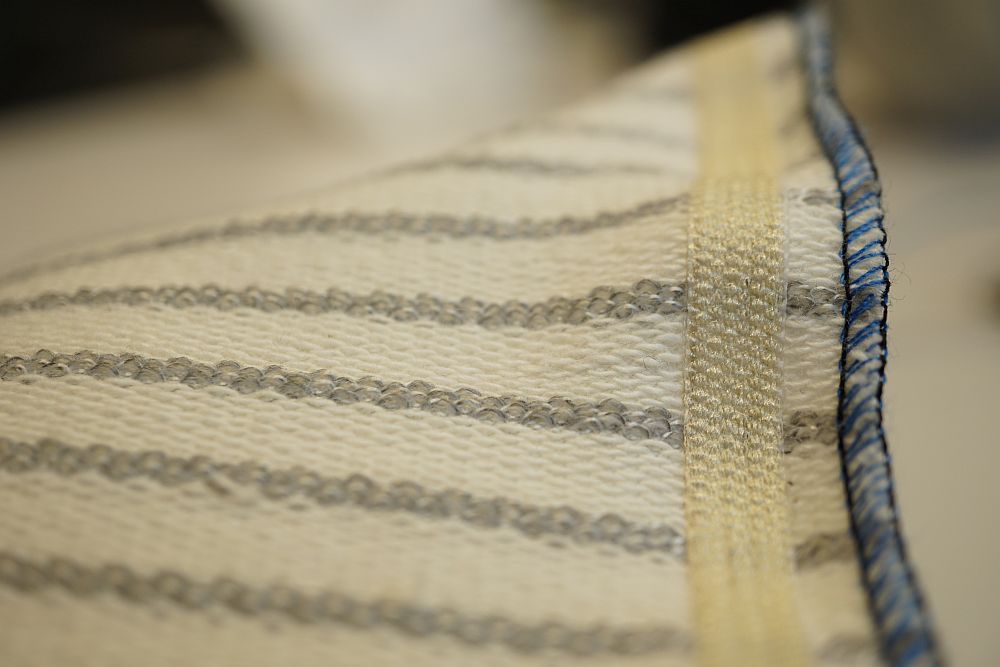
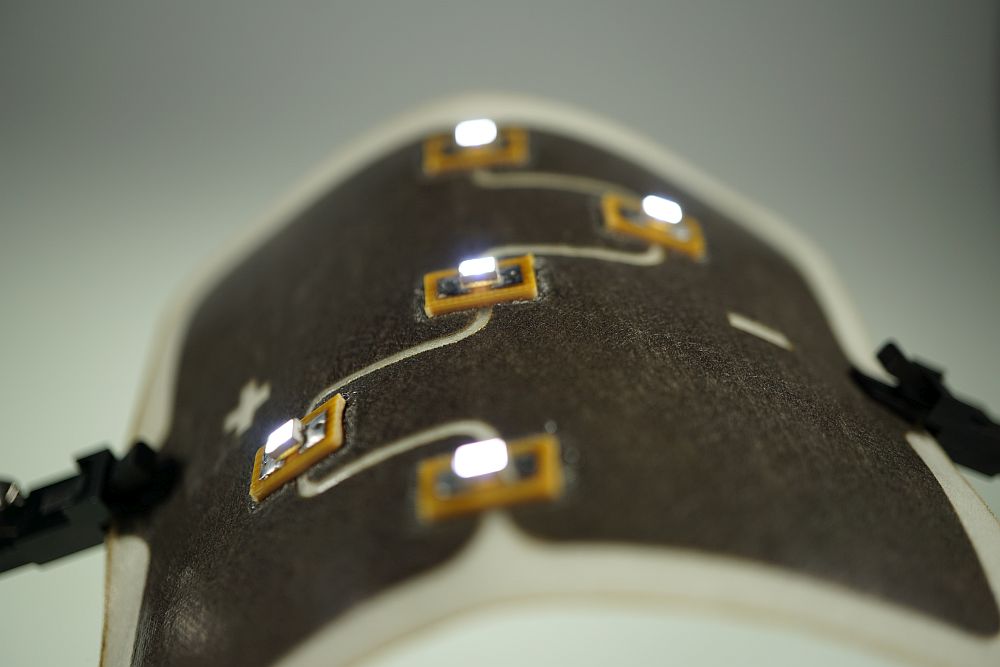
Ultrasonic plastic welding processes offer the advantage of interconnecting electrically conductive yarns or electronic modules with textile-integrated conductors using thermoplastic materials, thereby creating not only an electrical but also a mechanical contact at the same time. This eliminates the previously necessary steps of partially detaching conductor insulation and encapsulating the brittle solder contact. In the IGF project WelConTex2, developments and investigations were carried out for a reliable, economical integration technology for textiles with electronic functionality (e-textile) that is scalable in industrial production. Spot welding was used for the contacting of embroidered or knitted metal-polymer hybrid yarns, metallised polymer yarns or printed electronics as well as for the integration of electronic assemblies in textiles and for the realisation of via’s for multi-layer thermoplastic circuit boards. Continuous roll seam welding was used in the project for contacting conductive tapes with textile conductors for large-area heating and sensor textiles. In the project, solutions for suitable welding tools, process parameters as well as design guidelines for different material combinations were developed and the contact mechanisms were investigated. Furthermore, reliability tests and analytics were used to understand the ageing mechanisms and thus the long-term stability of the connection, considering electronic and textile standards.
SMEs benefit from the results in that a new efficient, resource-saving as well as reliable joining technique was developed for a variety of contacting variants in the production of e-textiles. The processes developed in the project offer great savings potential compared to previously used technologies, as the ultrasonic welding processes can be carried out both more economically and with less use of resources (energy, material). Thus, for the first time, suitable interconnection technologies are available to SMEs for the development and production of innovative e-textile applications in a large growth market. Due to the already existing equipment and know-how for ultrasonic welding in the textile industry as well as qualified workers, the technology transfer to industrial partners can be considered realistic in the short to medium term.