APPLAUSE for low-cost manufacturing of photonics, optics and electronics
In the design and manufacture of a wide range of electronic devices, such as smartphones and self-driving vehicles, new and expanded functionalities must constantly be accommodated in the smallest possible space. Advanced packaging – complex assembly and interconnection technology for semiconductor components – has emerged as an essential technology for the integration of photonics, optics and electronics. In the ongoing EU project APPLAUSE, the participants are focusing on the development of new tools, methods and processes for the mass production of electronic and optical components in high volumes using this technology. Fraunhofer IZM is involved in three of the six use cases.
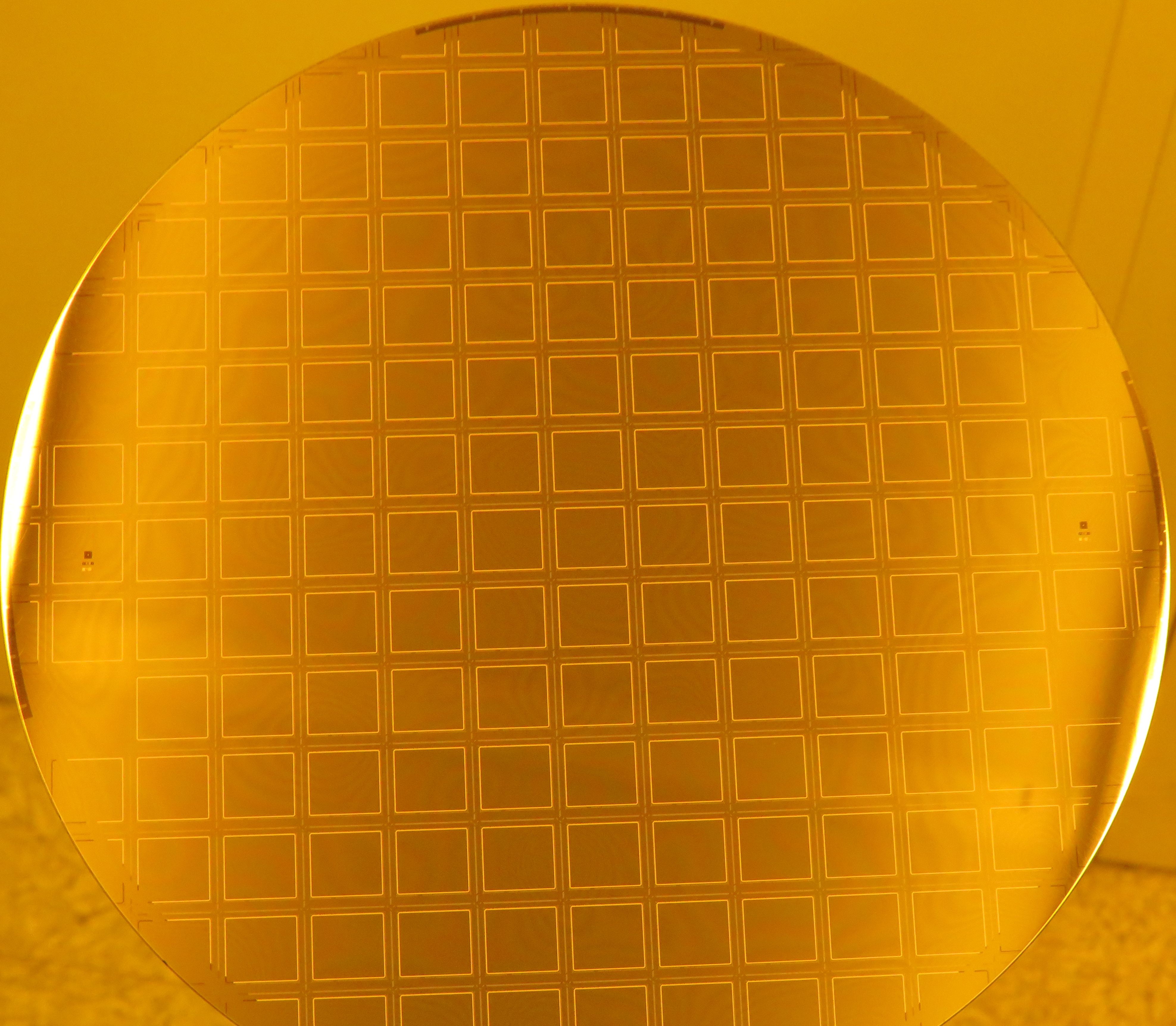
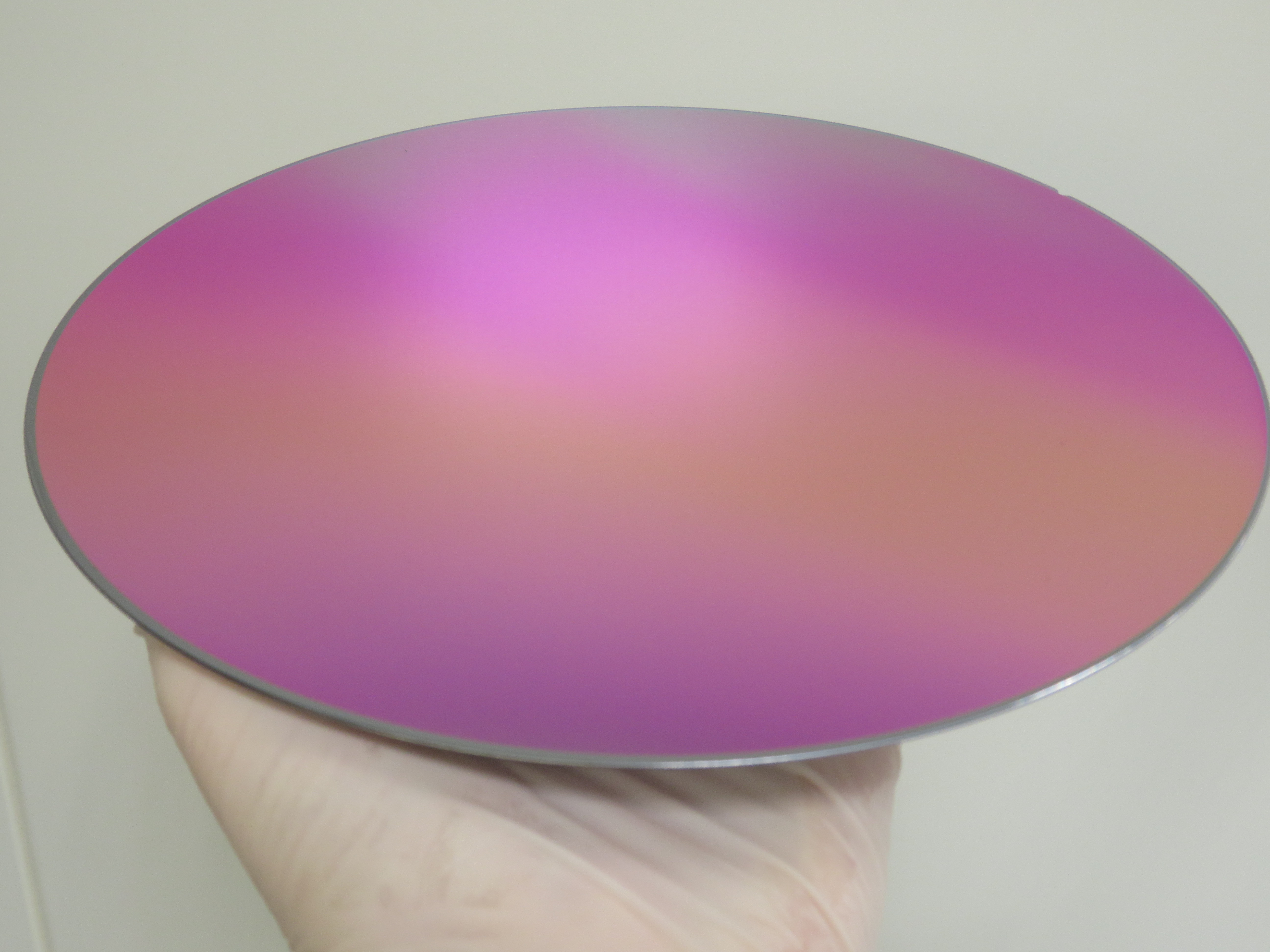
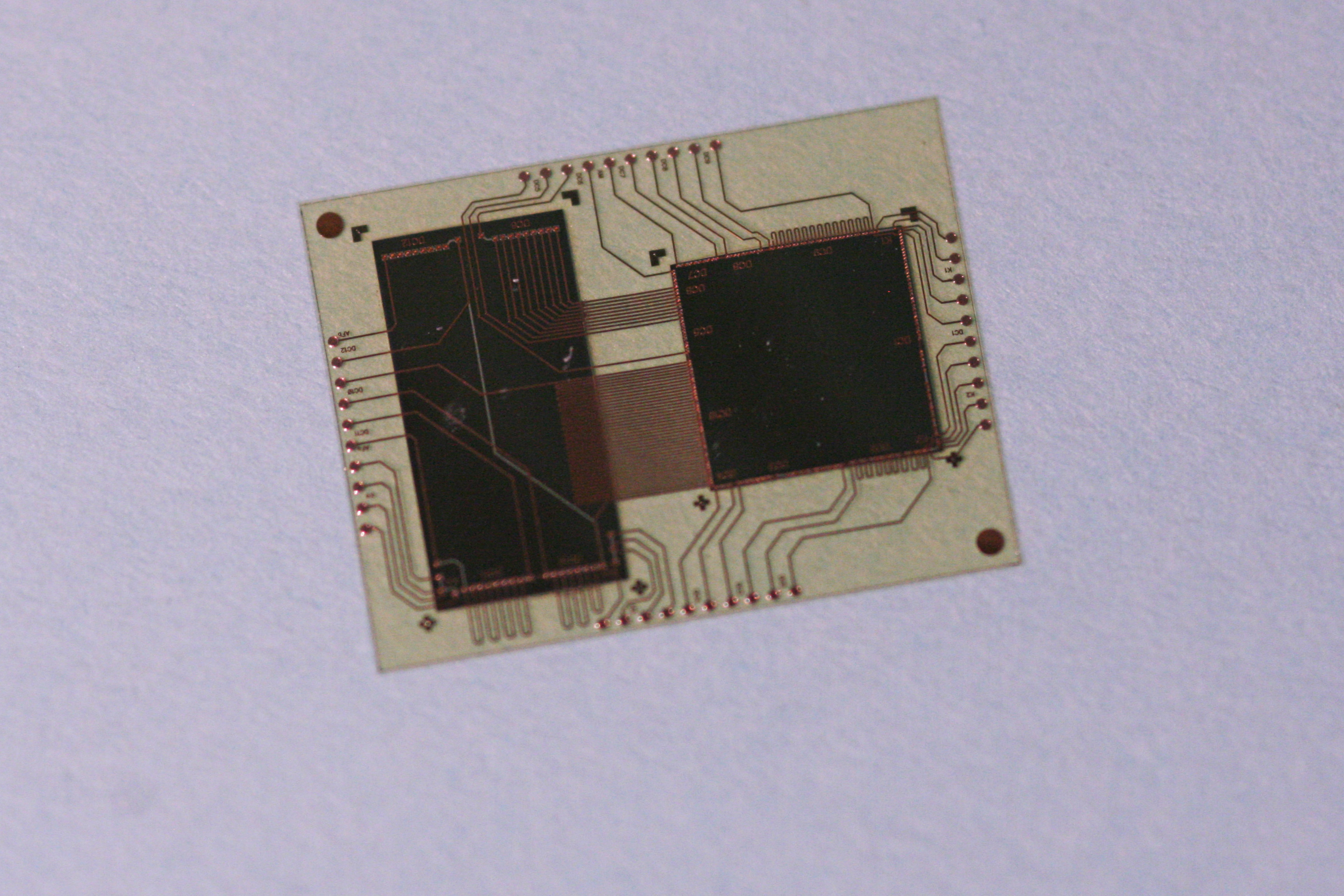
A consortium consisting of 31 key European players from the electronic packaging, optics and photonics sectors, leading equipment suppliers and test experts is driving the project "Advanced packaging for photonics, optics and electronics for low-cost manufacturing in Europe", or APPLAUSE for short. The project advances the European semiconductor value chain by developing new tools, methods and processes for highvolume manufacturing.
For the APPLAUSE project the Fraunhofer Institute for Reliability and Microintegration IZM has partnered with 12 large companies, 11 small and medium-sized enterprises and 7 research and technology organizations. In addition to various other exciting projects, the researchers in Berlin are involved in three industrial application fields, where they are working on the creation of
- a low-cost infrared camera for automotive and surveillance applications,
- of a high-speed datacom transceiver and
- of a flexible patch for cardiac monitoring.
Safer in traffic thanks to thermal infrared sensor
In the first use case, the consortium partners are developing a camera for automotive and security applications to generate thermal images with increased video rates and VGA resolution using a low-cost microbolometer. A microbolometer is a thermal sensor for detecting electromagnetic radiation, such as in situations where visible light is no longer sufficient. The microbolometer consists of a multi-layered yet ultra-thin membrane on which, among other things, an infrared-sensitive absorber layer is located. The membrane is suspended in a vacuum with two tiny electrodes and is thus thermally isolated. The incident infrared radiation heats the thermally insulated membrane by resonance, which leads to a change in the electrical resistance of the sensor layer. This changes the measurement signal and is detected by a readout circuit. Since the individual membranes are located in a two-dimensional grid on the readout circuit, a pixel matrix is formed. The result is a camera sensor for capturing infrared images.
The goal of this project is to fabricate a low-cost, high-performance thermal infrared sensor. Since a vacuum environment is required for the microbolometers to function properly, the researchers at Fraunhofer IZM use a special packaging process for robust hermetic encapsulation. In doing so, they cover the fine close-packed microbolometer structures at the wafer level with a cap wafer that has windows for infrared transmission. This not only protects the highly sensitive sensor elements for further integration into the final camera sensor, but also seals them hermetically gas-tight under vacuum for their complete function.
Faster data communication with high-speed transceivers
The second use case is about communicating and analyzing data. Here, ever higher speeds are a constant driver for further developments. Therefore, a low-cost 400 Gb/s high-speed optical transceiver for data communications is one of the next milestones in this field.
For this purpose, Fraunhofer IZM is developing an ambitious optical silicon bank for the transmitting unit (transceiver). The special feature here is the targeted passive adjustment of the components, which is intended to shorten and simplify the submicrometric, high-precision assembly for high volumes. Assembly costs could thus be significantly reduced compared to the current state of the art. By combining silicon microstructuring and gold-based metallizations for high-frequency signal rewiring and flip-chip solder contacts, a 3D substrate for optical elements (lens, isolator, fiber) including mechanical stoppers is fabricated. This allows the laser emitting device (EML) to be mounted with a precision of less than 1 μm. The approach benefits from the close cooperation with ALMAE Technologies in the project. Another exploratory approach to integrating optical elements is a 3D printed substrate, which is being tested in parallel.
Biocompatible patches diagnose directly on the skin
The digital age is also driving the development of surveillance technologies through wearables such as fitness trackers and smartwatches. But cardiologists still need alternative technologies for their diagnostic and monitoring tasks. This is where flexible electronics come into play. Such monitoring devices require close contact with the skin. Electronic components must be integrated into flexible and even stretchable layers that can adapt ideally to the skin. Fraunhofer IZM's third contribution to APPLAUSE therefore deals with the integration of thin devices into a thin and flexible polymer substrate including a redistribution layer. The technologies developed for stretchable electronics based on thermoplastic polyurethane will make it possible to integrate electrodes and electronics into a compact, flexible and biocompatible patch.
The outlined use cases clearly illustrate the great potential of advanced packaging technologies for the future of electronic systems. In the overall project, the expected impact is an increase in sales of over €300 million by 2025. The three-year APPLAUSE project is co-funded by the EU under Horizon 2020 and national funding agencies and industry as part of the Electronics Components and Systems for European Leadership Joint Undertaking (ECSEL JU) with €34 million.
Download
APPLAUSE has received funding from the ECSEL JU under grant agreement No 826588. The JU receives support from the European Union’s Horizon 2020 research and innovation programme as well as Belgium, Germany, Netherlands, Finland, Austria, France, Hungary, Latvia, Norway, Switzerland and Israel.
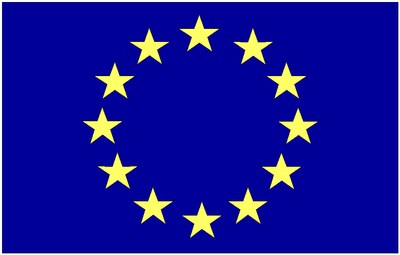
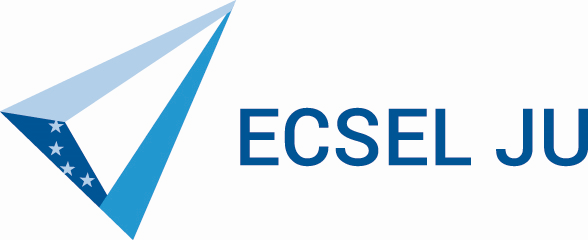
Last modified: