Test and reliability
Apart from ensuring the best possible system design, understanding material, mechanical and thermomechanical behavior on package, component and module levels is critical for ensuring overall system reliability. Thermally and thermo-mechanically induced failure mechanisms can lead to premature failure and limit lifetime.
Smaller package dimension result in shorter diffusion outlets for external humidity stress. This can result in increased electro-chemical degradation mechanisms, that usually lead to failure and thus a shorter lifetime of the electrical circuits. For this reason it is very important that crucial parameters such as (extreme) operating conditions with system-level impact (e.g. operating temperatures and humidity) are already modeled and then optimized in the early stages of the design process. The aim is maximizing reliability while keeping cost and effort low.
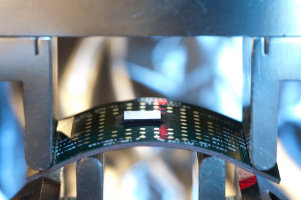